Specification
anodized aluminum strip for transformer winding
Source:Original
Editing:frank
Time:2022-02-15 18:07
In recent years, there are more than 10,000 transformers in the United States that are equipped with aluminum coils on the low-voltage side, which can work continuously in the distribution network. More than 20,000 tons of aluminum strip are used in transformers every year. Similarly, some electrical companies in Europe also mass-produce transformers with aluminum coils.
The application of oversized components is currently being studied. The transformer is not only required to have high power, but also low noise. In order to achieve these two requirements, the high-voltage and low-voltage aluminum coils can be cast with resin to make dry-type transformers.
In addition, magnet jacks, speakers, reactors, electromagnetic clutches, magnetic field coils and, more recently, magnetic pads for aerial ropeways are equipped with aluminum ribbon coils, Individual aluminum round and flat coils are also used, such as starters and special transformers for automobiles, and the largest application area is transformers for distribution networks.
On dry-type transformers, most high-voltage and low-voltage coils are made of aluminum strip material
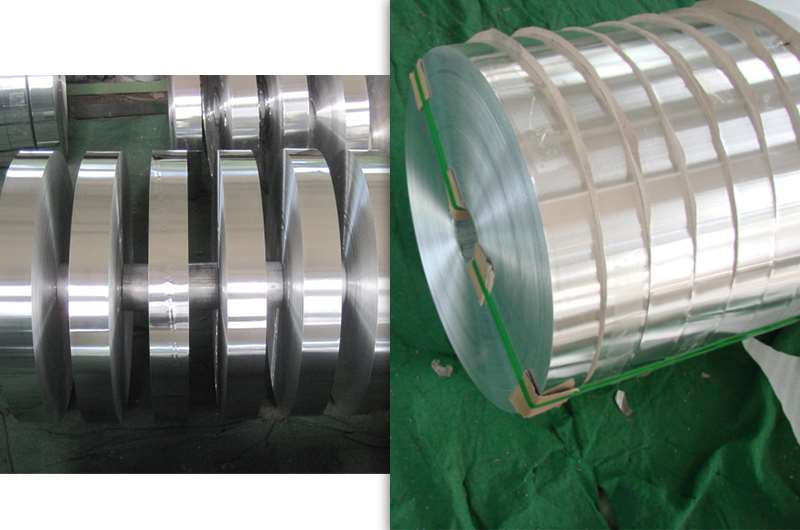
.
On oil or crophenol transformers, only low-voltage coils are made of aluminum strips. Compared with copper coils with the same conductivity, aluminum has the advantages of affordable price, light weight and small temperature rise. The disadvantage is that the coil gap is large. Compared with the linear coil, the strip coil has the advantages of small footprint and simple winding technology. Can eliminate or reduce axial short-circuit power, good thermal conductivity, and low requirements for insulation.
Individual coils installed need to have a minimum winding gap. The use of copper strip is very expensive for conductive materials. The reason for using aluminum strip is economic: not only because the raw materials are cheap, but also because the widely used mass-produced rolled semi-finished products are cheaper. But overall
The strip used in the transformer is only a relatively small part. The technical requirements of the coil for the strip are mainly high conductivity, good processing performance, dimensional tolerance that can meet the use requirements, appropriate edge state and appropriate finish.
Considering that the coil should have as high conductivity and processing performance as possible, the only material that can be selected is pure aluminum, or in special cases, such as anodized aluminum strip for transformer winding with small thickness, pure aluminum in semi-hard or hard state should be used. In this way, the brittle oxide film formed by anodic oxidation can be avoided, and the strip will be deformed greatly when winding the coil, and the oxide film will crack. The thickness of the strip used for the coil is about
The thickness of the strip used for the anodized aluminum strip for transformer winding coil is about 0.2-4.0 mm and the width is 20-1500 mm. In most cases, the allowable dimensional deviation is approximately supplemented by the average value of the deviation calculated by the thickness. Therefore, the coil resistance can be calculated accurately and the coil gap can be determined in advance. The shear burr of the strip and foreign particles on the surface can damage the insulation, so it must be cleaned according to the thickness, insulation type, edge state and original shear condition of the strip. When the strip is cut, a cutter with appropriate shape shall be used to make the shear burr perpendicular to the surface of the strip and make it less than 50 microns. The electrical connection of the coil is through cold extrusion welding or gas shielded welding or slotting and pressing at the end of the strip. The most commonly used method is cold extrusion welding.
Anodized aluminum strip for transformer winding coil is suitable for manufacturing equipment with small inter turn voltage, which is the lightest and occupies a small area. Anodized aluminum strip coils are also suitable for chokes, lifting magnets, power tools, magnetic couplers, and electromagnetic devices for cars and elevators. The hard insulating layer of alumina can be produced by special anodizing method. The insulation is only a few microns thick. According to different belt thickness, the utilization rate of winding gap can reach 97%. Since the coil of anodized strip can not only withstand high temperature, but also bear large load, the weight per unit power is small.
The application of oversized components is currently being studied. The transformer is not only required to have high power, but also low noise. In order to achieve these two requirements, the high-voltage and low-voltage aluminum coils can be cast with resin to make dry-type transformers.
In addition, magnet jacks, speakers, reactors, electromagnetic clutches, magnetic field coils and, more recently, magnetic pads for aerial ropeways are equipped with aluminum ribbon coils, Individual aluminum round and flat coils are also used, such as starters and special transformers for automobiles, and the largest application area is transformers for distribution networks.
On dry-type transformers, most high-voltage and low-voltage coils are made of aluminum strip material
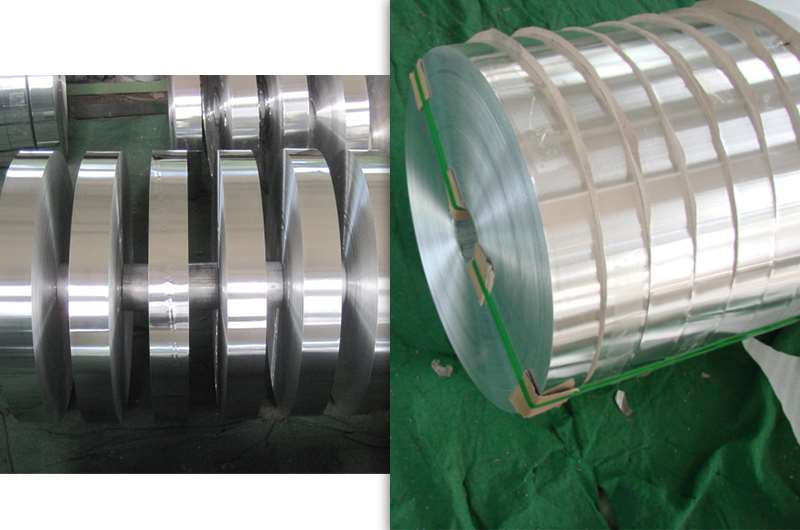
.
On oil or crophenol transformers, only low-voltage coils are made of aluminum strips. Compared with copper coils with the same conductivity, aluminum has the advantages of affordable price, light weight and small temperature rise. The disadvantage is that the coil gap is large. Compared with the linear coil, the strip coil has the advantages of small footprint and simple winding technology. Can eliminate or reduce axial short-circuit power, good thermal conductivity, and low requirements for insulation.
Individual coils installed need to have a minimum winding gap. The use of copper strip is very expensive for conductive materials. The reason for using aluminum strip is economic: not only because the raw materials are cheap, but also because the widely used mass-produced rolled semi-finished products are cheaper. But overall
The strip used in the transformer is only a relatively small part. The technical requirements of the coil for the strip are mainly high conductivity, good processing performance, dimensional tolerance that can meet the use requirements, appropriate edge state and appropriate finish.
Considering that the coil should have as high conductivity and processing performance as possible, the only material that can be selected is pure aluminum, or in special cases, such as anodized aluminum strip for transformer winding with small thickness, pure aluminum in semi-hard or hard state should be used. In this way, the brittle oxide film formed by anodic oxidation can be avoided, and the strip will be deformed greatly when winding the coil, and the oxide film will crack. The thickness of the strip used for the coil is about
The thickness of the strip used for the anodized aluminum strip for transformer winding coil is about 0.2-4.0 mm and the width is 20-1500 mm. In most cases, the allowable dimensional deviation is approximately supplemented by the average value of the deviation calculated by the thickness. Therefore, the coil resistance can be calculated accurately and the coil gap can be determined in advance. The shear burr of the strip and foreign particles on the surface can damage the insulation, so it must be cleaned according to the thickness, insulation type, edge state and original shear condition of the strip. When the strip is cut, a cutter with appropriate shape shall be used to make the shear burr perpendicular to the surface of the strip and make it less than 50 microns. The electrical connection of the coil is through cold extrusion welding or gas shielded welding or slotting and pressing at the end of the strip. The most commonly used method is cold extrusion welding.
Anodized aluminum strip for transformer winding coil is suitable for manufacturing equipment with small inter turn voltage, which is the lightest and occupies a small area. Anodized aluminum strip coils are also suitable for chokes, lifting magnets, power tools, magnetic couplers, and electromagnetic devices for cars and elevators. The hard insulating layer of alumina can be produced by special anodizing method. The insulation is only a few microns thick. According to different belt thickness, the utilization rate of winding gap can reach 97%. Since the coil of anodized strip can not only withstand high temperature, but also bear large load, the weight per unit power is small.
RELATED READ:
- Foil for electrolytic capacitors2015.3.19
- Copper-Clad Aluminum Wire (CCA)2015.3.19
- 5052 aluminum strip for shutters2015.3.19
- Application of aluminum semi-finished products in e2015.3.19
- Copper clad aluminum enamelled round wire2015.3.19