Specification
copper clad aluminum enamelled wire used in fan motor
Source:Original
Editing:frank
Time:2021-08-24 18:10
Motor windings for fans account for a large proportion of motor costs. Therefore, in today's soaring copper prices, using cheaper alternatives than traditional pure copper windings has become the first choice for motor enterprises to tap potential.
1 copper clad aluminum enamelled wire used in fan motor
1.1 light weight and remarkable economy
The copper density is about 8.89g/cm3 and the aluminum density is about 2.69g/cm3. The proportion of copper area in the cross section of copper-clad aluminum enamelled wire is usually 10% ~ 15%. If calculated by 15%, it is 8.89/2.69 ×( 1-0.15) ≈ 2.8, that is, under the same weight, the theoretical wire length of copper-clad aluminum enamelled wire of the same specification is about 2.8 times that of pure copper enamelled wire.
1.2 the conductivity is close to that of pure copper enamelled wire
According to the physical skin effect, the alternating current is not evenly distributed in the conductor according to the conductor section, but concentrated on the conductor surface. According to this inference, if copper within a certain radius along the axis of pure copper enamelled wire is replaced with aluminum with higher resistivity, the maximum current load of the whole conductor decreases little, that is, the conductivity basically does not decrease.
1.3 the production process of the original pure copper enamelled wire can continue to be applied
The outer layer of copper clad aluminum enamelled wire used in fan motor is also pure copper, so the contact resistance at the connecting end remains unchanged, and the weldability is the same as that of pure copper enamelled wire. Therefore, the welding and other production processes originally applied to pure copper enamelled wire can continue to be used.
2. Technical difficulties in the application of copper clad aluminum enabled wire used in fan motor
2.1 reliability reduction of winding solder joints
Tin welding is a common welding method for fan motor winding joints. Its characteristics are: low temperature, easy operation, local overheating, little impact on the surrounding insulating paint, low cost, but low mechanical strength. Although it can be applied to copper-clad aluminum enamelled wire, compared with pure copper enamelled wire, it has the following shortcomings:
① There are inevitable poor welding problems in some welding joints.
Aluminum oxidizes rapidly in the air, and a layer of oxide protective film with dense structure will be formed on the surface, which makes it difficult for the aluminum containing section in the circular section of copper-clad aluminum enamelled wire to form alloy with solder, resulting in gap on the welding surface. Under the influence of repeated stress, it is easy to reduce the bearing capacity of welded joint section.
② Low temperature fatigue strength. The poor conductivity of alumina may lead to increased heating of solder joints due to increased resistance. The increase of the overall temperature of the solder joint will also lead to the increase of the temperature mechanical stress and the decrease of the fatigue strength of the solder joint.
③ A section of copper-clad aluminum enamelled wire near the solder joint will age and fracture prematurely. The melting point of aluminum is lower than that of copper. During the welding process, a section of copper-clad aluminum enamelled wire close to the welding point will cause damage to the insulating paint and oxidation of some metals due to local high temperature. At the same time, it is also forced to accept a annealing heat treatment, and its performance index will be greatly reduced. The decline degree of performance index depends on the welding temperature, the length of welding time, the quality of copper-clad aluminum enamelled wire and tin wire, working environment and so on.
④ The thermal expansion coefficient of materials varies greatly. At the solder joint, due to the coexistence of copper, aluminum, alumina and other materials, the thermal expansion coefficient of alumina is 6.4 μ M / m. ℃, 17.2 for copper μ M / m. ℃, aluminum up to 23 μ m/m.℃。 Different expansion coefficients will increase the stress and strain of copper-clad aluminum enamelled wire in and near the welding point and shorten the service life.
2.2 the motor needs to be replaced with large slot magnetic core
The DC resistivity of copper-clad aluminum enamelled wire is about 1.5 times that of pure copper wire; When the resistance value is the same, the wire diameter is about 1.2 times that of pure copper. In other words, in order to achieve the same resistance value, a larger copper-clad aluminum enamelled wire is required. When the number of turns remains unchanged, the volume of coil winding will increase by about 20%.
2.3 it is necessary to increase the capital investment in the technical transformation of production equipment and the training of production workers
The tensile strength of copper-clad aluminum enamelled wire is lower than that of pure copper enamelled wire. In the production process, excessive tension or slightly higher tension in the high-speed winding machine will cause the copper-clad aluminum enamelled wire to break and become waste. However, it has been proved that skilled workers and high-speed winding machines that can maintain stable tension can reduce the waste rate gap between the two to a great extent.
3 solution
3.1 reliable conductor connection mode shall be adopted
A reliable connection method is to adopt mechanical fastening, but the disadvantage is to increase the connecting parts and increase the cost of raw materials. At the same time, it does not make good use of the characteristic that the weldability of copper-clad aluminum enamelled wire is the same as that of pure copper enamelled wire. Therefore, the following methods to improve the welding production process can be adopted: try to reduce the temperature in the welding process, such as reducing the temperature of tin furnace; Reduce the high temperature time in the welding process, such as removing the insulating paint mechanically; Select highly skilled production workers; Try to reduce the ambient temperature of the welding station, such as adding cold air cooling measures.
3.2 select high-quality copper clad aluminum enabled wire used in fan motor
Due to the obvious price advantage, many enterprises produce copper-clad aluminum enamelled wire, but the quality is uneven. Therefore, we should pay attention to the quality of insulating paint and metal layer of copper-clad aluminum enamelled wire.
3.3 need to increase production investment
In order to reduce the wire breakage rate during winding, it is required that the starting performance of the winding machine is stable and the winding speed is stable, so as to ensure that the tension of each steering node in the enamelled wire winding process is not large, which requires the enterprise to replace or upgrade the production equipment such as the winding machine that fails to meet the requirements. It is true that the above measures will increase the manufacturing cost when applying copper-clad aluminum enamelled wire in fan motor, but its price advantage can reduce the manufacturing cost. In addition, with the strong market demand for copper-clad aluminum enamelled wire, the cost of its production equipment will be gradually reduced, the increasing maturity and improvement of the production process will also lead to the decline of its processing cost, and the reduction of the final price of the product will make it more competitive in the market.
1 copper clad aluminum enamelled wire used in fan motor
1.1 light weight and remarkable economy
The copper density is about 8.89g/cm3 and the aluminum density is about 2.69g/cm3. The proportion of copper area in the cross section of copper-clad aluminum enamelled wire is usually 10% ~ 15%. If calculated by 15%, it is 8.89/2.69 ×( 1-0.15) ≈ 2.8, that is, under the same weight, the theoretical wire length of copper-clad aluminum enamelled wire of the same specification is about 2.8 times that of pure copper enamelled wire.
1.2 the conductivity is close to that of pure copper enamelled wire
According to the physical skin effect, the alternating current is not evenly distributed in the conductor according to the conductor section, but concentrated on the conductor surface. According to this inference, if copper within a certain radius along the axis of pure copper enamelled wire is replaced with aluminum with higher resistivity, the maximum current load of the whole conductor decreases little, that is, the conductivity basically does not decrease.
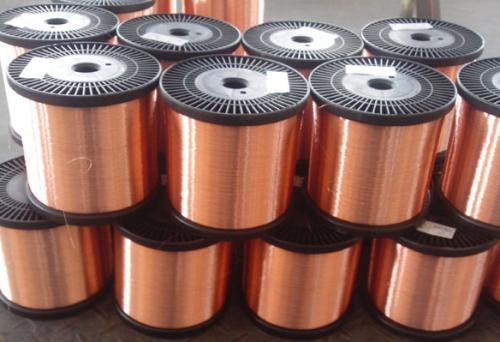
1.3 the production process of the original pure copper enamelled wire can continue to be applied
The outer layer of copper clad aluminum enamelled wire used in fan motor is also pure copper, so the contact resistance at the connecting end remains unchanged, and the weldability is the same as that of pure copper enamelled wire. Therefore, the welding and other production processes originally applied to pure copper enamelled wire can continue to be used.
2. Technical difficulties in the application of copper clad aluminum enabled wire used in fan motor
2.1 reliability reduction of winding solder joints
Tin welding is a common welding method for fan motor winding joints. Its characteristics are: low temperature, easy operation, local overheating, little impact on the surrounding insulating paint, low cost, but low mechanical strength. Although it can be applied to copper-clad aluminum enamelled wire, compared with pure copper enamelled wire, it has the following shortcomings:
① There are inevitable poor welding problems in some welding joints.
Aluminum oxidizes rapidly in the air, and a layer of oxide protective film with dense structure will be formed on the surface, which makes it difficult for the aluminum containing section in the circular section of copper-clad aluminum enamelled wire to form alloy with solder, resulting in gap on the welding surface. Under the influence of repeated stress, it is easy to reduce the bearing capacity of welded joint section.
② Low temperature fatigue strength. The poor conductivity of alumina may lead to increased heating of solder joints due to increased resistance. The increase of the overall temperature of the solder joint will also lead to the increase of the temperature mechanical stress and the decrease of the fatigue strength of the solder joint.
③ A section of copper-clad aluminum enamelled wire near the solder joint will age and fracture prematurely. The melting point of aluminum is lower than that of copper. During the welding process, a section of copper-clad aluminum enamelled wire close to the welding point will cause damage to the insulating paint and oxidation of some metals due to local high temperature. At the same time, it is also forced to accept a annealing heat treatment, and its performance index will be greatly reduced. The decline degree of performance index depends on the welding temperature, the length of welding time, the quality of copper-clad aluminum enamelled wire and tin wire, working environment and so on.
④ The thermal expansion coefficient of materials varies greatly. At the solder joint, due to the coexistence of copper, aluminum, alumina and other materials, the thermal expansion coefficient of alumina is 6.4 μ M / m. ℃, 17.2 for copper μ M / m. ℃, aluminum up to 23 μ m/m.℃。 Different expansion coefficients will increase the stress and strain of copper-clad aluminum enamelled wire in and near the welding point and shorten the service life.
2.2 the motor needs to be replaced with large slot magnetic core
The DC resistivity of copper-clad aluminum enamelled wire is about 1.5 times that of pure copper wire; When the resistance value is the same, the wire diameter is about 1.2 times that of pure copper. In other words, in order to achieve the same resistance value, a larger copper-clad aluminum enamelled wire is required. When the number of turns remains unchanged, the volume of coil winding will increase by about 20%.
2.3 it is necessary to increase the capital investment in the technical transformation of production equipment and the training of production workers
The tensile strength of copper-clad aluminum enamelled wire is lower than that of pure copper enamelled wire. In the production process, excessive tension or slightly higher tension in the high-speed winding machine will cause the copper-clad aluminum enamelled wire to break and become waste. However, it has been proved that skilled workers and high-speed winding machines that can maintain stable tension can reduce the waste rate gap between the two to a great extent.
3 solution
3.1 reliable conductor connection mode shall be adopted
A reliable connection method is to adopt mechanical fastening, but the disadvantage is to increase the connecting parts and increase the cost of raw materials. At the same time, it does not make good use of the characteristic that the weldability of copper-clad aluminum enamelled wire is the same as that of pure copper enamelled wire. Therefore, the following methods to improve the welding production process can be adopted: try to reduce the temperature in the welding process, such as reducing the temperature of tin furnace; Reduce the high temperature time in the welding process, such as removing the insulating paint mechanically; Select highly skilled production workers; Try to reduce the ambient temperature of the welding station, such as adding cold air cooling measures.
3.2 select high-quality copper clad aluminum enabled wire used in fan motor
Due to the obvious price advantage, many enterprises produce copper-clad aluminum enamelled wire, but the quality is uneven. Therefore, we should pay attention to the quality of insulating paint and metal layer of copper-clad aluminum enamelled wire.
3.3 need to increase production investment
In order to reduce the wire breakage rate during winding, it is required that the starting performance of the winding machine is stable and the winding speed is stable, so as to ensure that the tension of each steering node in the enamelled wire winding process is not large, which requires the enterprise to replace or upgrade the production equipment such as the winding machine that fails to meet the requirements. It is true that the above measures will increase the manufacturing cost when applying copper-clad aluminum enamelled wire in fan motor, but its price advantage can reduce the manufacturing cost. In addition, with the strong market demand for copper-clad aluminum enamelled wire, the cost of its production equipment will be gradually reduced, the increasing maturity and improvement of the production process will also lead to the decline of its processing cost, and the reduction of the final price of the product will make it more competitive in the market.
Previous :enameled aluminium wire
RELATED READ:
- Foil for electrolytic capacitors2015.3.19
- Copper-Clad Aluminum Wire (CCA)2015.3.19
- 5052 aluminum strip for shutters2015.3.19
- Application of aluminum semi-finished products in e2015.3.19
- Copper clad aluminum enamelled round wire2015.3.19