Specification
transformer aluminum wire
Source:Original
Editing:frank
Time:2020-07-20 16:20
The application of transformer aluminum wire in transformers is very common in European and American countries, because the price of aluminum is much cheaper than copper, and the density of aluminum is much smaller than that of copper. In the case of the same cross section, aluminum is much lighter than copper. The resistivity at 20°C is copper: 0.017241Ω·mm2/m; aluminum: 0.02801Ω·mm2/m. As long as the aluminum with a larger cross-section is selected, the same or even lower loss value as copper can be guaranteed.
For epoxy resin cast dry-type transformers, because the coefficient of thermal expansion and contraction of aluminum is closer to that of epoxy resin than copper, the crack resistance of transformer aluminum wire is better than that of copper winding. Moreover, since the mechanical strength of the dry epoxy resin casting winding itself is very good, there is no difference in mechanical strength between copper and aluminum.
Aluminum wire transformers can operate safely and reliably.
The IEC standards and national standards do not exclude aluminum as a conductor. In GB1094.5-2008 Item 4.1 and IEC60076-5:2006, the provisions and calculation methods for the heat resistance of copper windings and aluminum windings withstand short circuits are given. And related parameters, it can be analyzed that aluminum conductors can be used as transformer conductors.
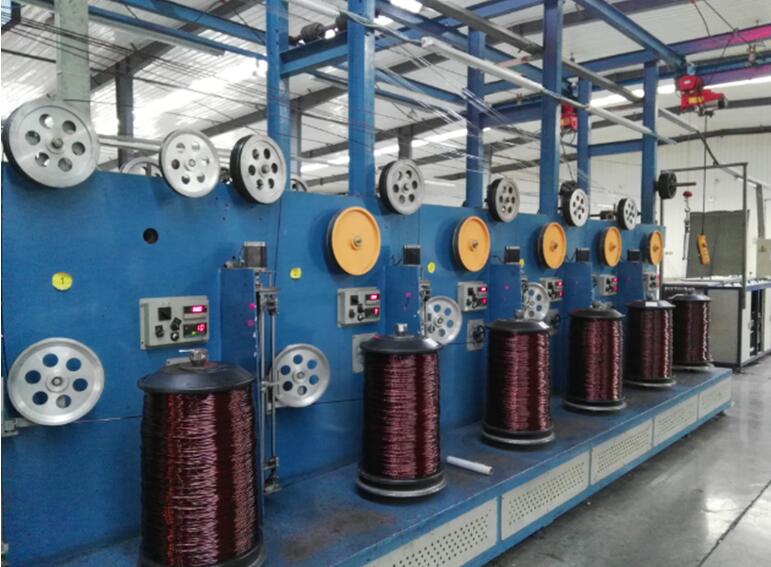
As long as the aluminum wire transformer can withstand the requirements of heat resistance during short-circuit current and can withstand the dynamic stability requirements of mechanical force during short-circuit, it is qualified. As long as the design is reasonable and the process must be adjusted accordingly, especially when the welding technology is advanced, it can achieve high temperature resistance (increased heat resistance) and low loss, and aluminum wire transformers will be widely used. Users must also have the corresponding understanding. Users think that aluminum wire transformers have a high temperature and short life, and they are afraid to use them. However, users praise the imported aluminum wire transformers and worry about domestic aluminum wire transformers. There must be a unified understanding between the transformer factory and the user, and the promotion and application of aluminum wire transformers can proceed smoothly.
Many transformer companies are already using transformer aluminum wire to produce transformers, especially epoxy cast dry-type transformers, whose windings are made of aluminum. The reason why our country has eliminated aluminum winding transformers is due to the small price difference between copper and aluminum in the 1980s and 1990s (less than 1:2, and now it is close to or more than 1:3). The external dimensions are small (because the conductor specifications used are smaller than aluminum), the silicon steel sheet is relatively saved, and the previous aluminum winding welding technology is not good enough, so the aluminum winding transformer is clearly eliminated.
At present, various power users have become accustomed to copper-winding transformers. Just because copper is more expensive than aluminum, they believe that copper is better than aluminum. Therefore, manufacturers that use aluminum wires are cutting corners. As a result, transformer manufacturers are afraid of being misunderstood and dare not use aluminum windings. In fact, this is unfair. As long as the technical parameters of the transformer are consistent, the use of copper or aluminum in the windings is the same for customers. Of course, the manufacturer must clearly tell the user what material the winding uses when quoting.
For epoxy resin cast dry-type transformers, because the coefficient of thermal expansion and contraction of aluminum is closer to that of epoxy resin than copper, the crack resistance of transformer aluminum wire is better than that of copper winding. Moreover, since the mechanical strength of the dry epoxy resin casting winding itself is very good, there is no difference in mechanical strength between copper and aluminum.
Aluminum wire transformers can operate safely and reliably.
The IEC standards and national standards do not exclude aluminum as a conductor. In GB1094.5-2008 Item 4.1 and IEC60076-5:2006, the provisions and calculation methods for the heat resistance of copper windings and aluminum windings withstand short circuits are given. And related parameters, it can be analyzed that aluminum conductors can be used as transformer conductors.
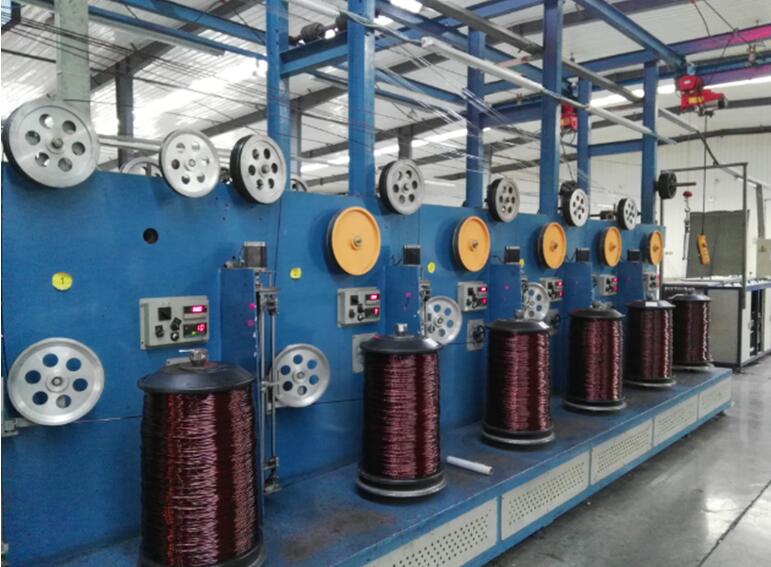
As long as the aluminum wire transformer can withstand the requirements of heat resistance during short-circuit current and can withstand the dynamic stability requirements of mechanical force during short-circuit, it is qualified. As long as the design is reasonable and the process must be adjusted accordingly, especially when the welding technology is advanced, it can achieve high temperature resistance (increased heat resistance) and low loss, and aluminum wire transformers will be widely used. Users must also have the corresponding understanding. Users think that aluminum wire transformers have a high temperature and short life, and they are afraid to use them. However, users praise the imported aluminum wire transformers and worry about domestic aluminum wire transformers. There must be a unified understanding between the transformer factory and the user, and the promotion and application of aluminum wire transformers can proceed smoothly.
Many transformer companies are already using transformer aluminum wire to produce transformers, especially epoxy cast dry-type transformers, whose windings are made of aluminum. The reason why our country has eliminated aluminum winding transformers is due to the small price difference between copper and aluminum in the 1980s and 1990s (less than 1:2, and now it is close to or more than 1:3). The external dimensions are small (because the conductor specifications used are smaller than aluminum), the silicon steel sheet is relatively saved, and the previous aluminum winding welding technology is not good enough, so the aluminum winding transformer is clearly eliminated.
At present, various power users have become accustomed to copper-winding transformers. Just because copper is more expensive than aluminum, they believe that copper is better than aluminum. Therefore, manufacturers that use aluminum wires are cutting corners. As a result, transformer manufacturers are afraid of being misunderstood and dare not use aluminum windings. In fact, this is unfair. As long as the technical parameters of the transformer are consistent, the use of copper or aluminum in the windings is the same for customers. Of course, the manufacturer must clearly tell the user what material the winding uses when quoting.
Previous :aluminum flat wire for transformers
RELATED READ:
- Foil for electrolytic capacitors2015.3.19
- Copper-Clad Aluminum Wire (CCA)2015.3.19
- 5052 aluminum strip for shutters2015.3.19
- Application of aluminum semi-finished products in e2015.3.19
- Copper clad aluminum enamelled round wire2015.3.19